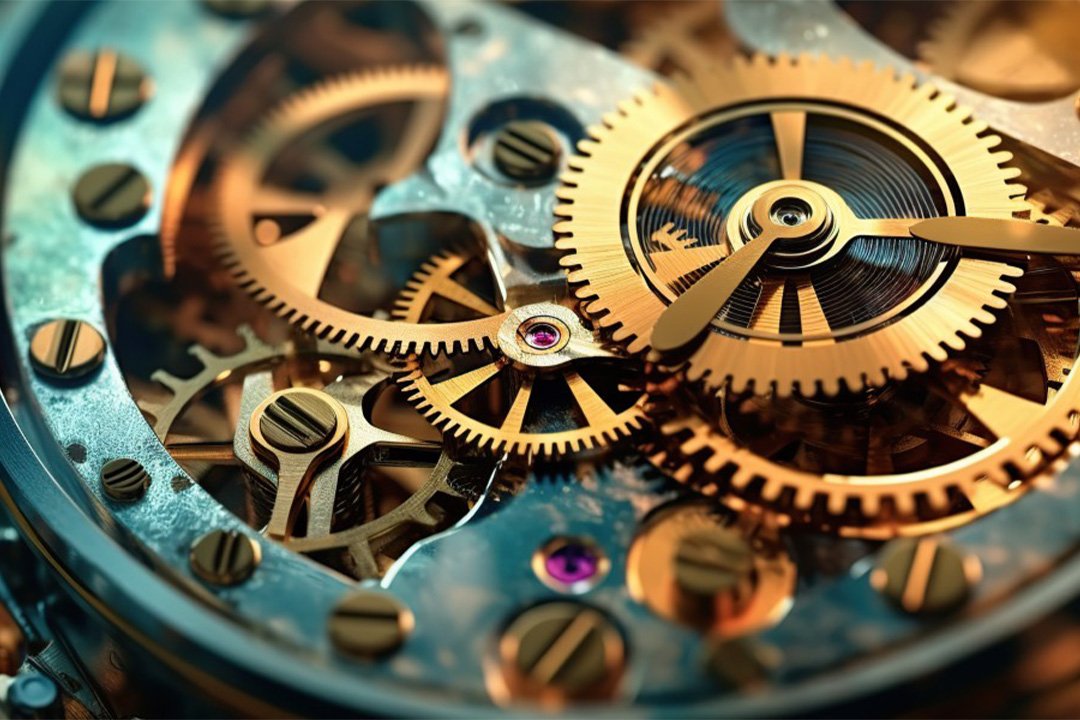
In my current role as an SAP EAM Consultant specializing in Customer Service (CS) at newITera, I am heavily involved in SAP implementation and deployment projects. In this capacity, I frequently encounter issues that do not have a standard SAP solution. This article highlights one such issue: the integration of SAP Warehouse Management (WM) within the CS repair process.
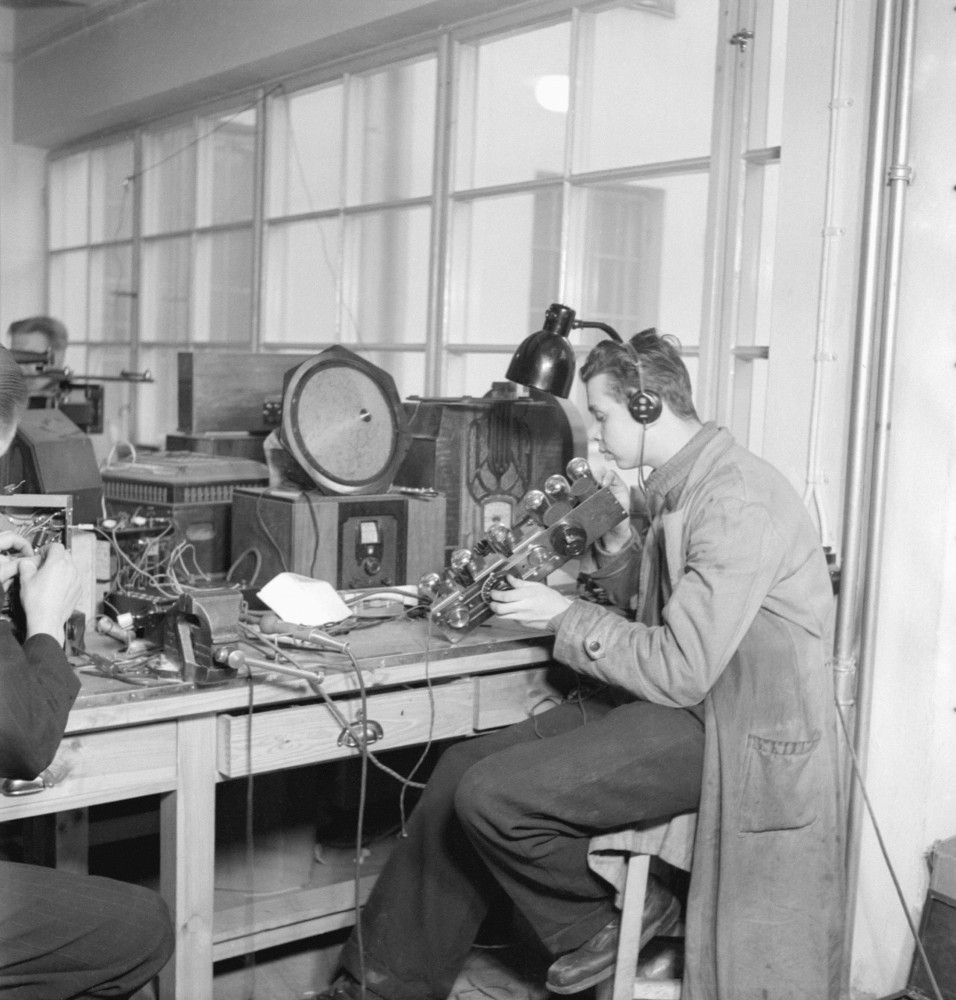
At large repair centers, where approximately 50 to 100 technicians are constantly repairing systems, maintaining oversight can be challenging. Devices may be stored or repaired in various locations – in different parts of the workshop or even in separate buildings. Additionally, repairs can sometimes take longer than expected, perhaps due to a shortage of spare parts or waiting for customer approval on a quote.
Furthermore, spare parts are often stored in an open warehouse, allowing technicians to pick the parts they need. This can lead to inaccuracies in inventory records. Spare parts may also have special statuses or be subject to expiration dates, which SAP handles through a batch determination strategy.
The solution to these challenges lies in integrating WM into the repair process. With WM, we can record the location of a device (material and batch) and utilize its extensive functionalities for better management of the spare parts inventory.
We have leveraged the benefits of WM by developing a custom process that integrates WM functionalities with CS processes. This was accomplished with a multidisciplinary team of CS and WM consultants at a client site.
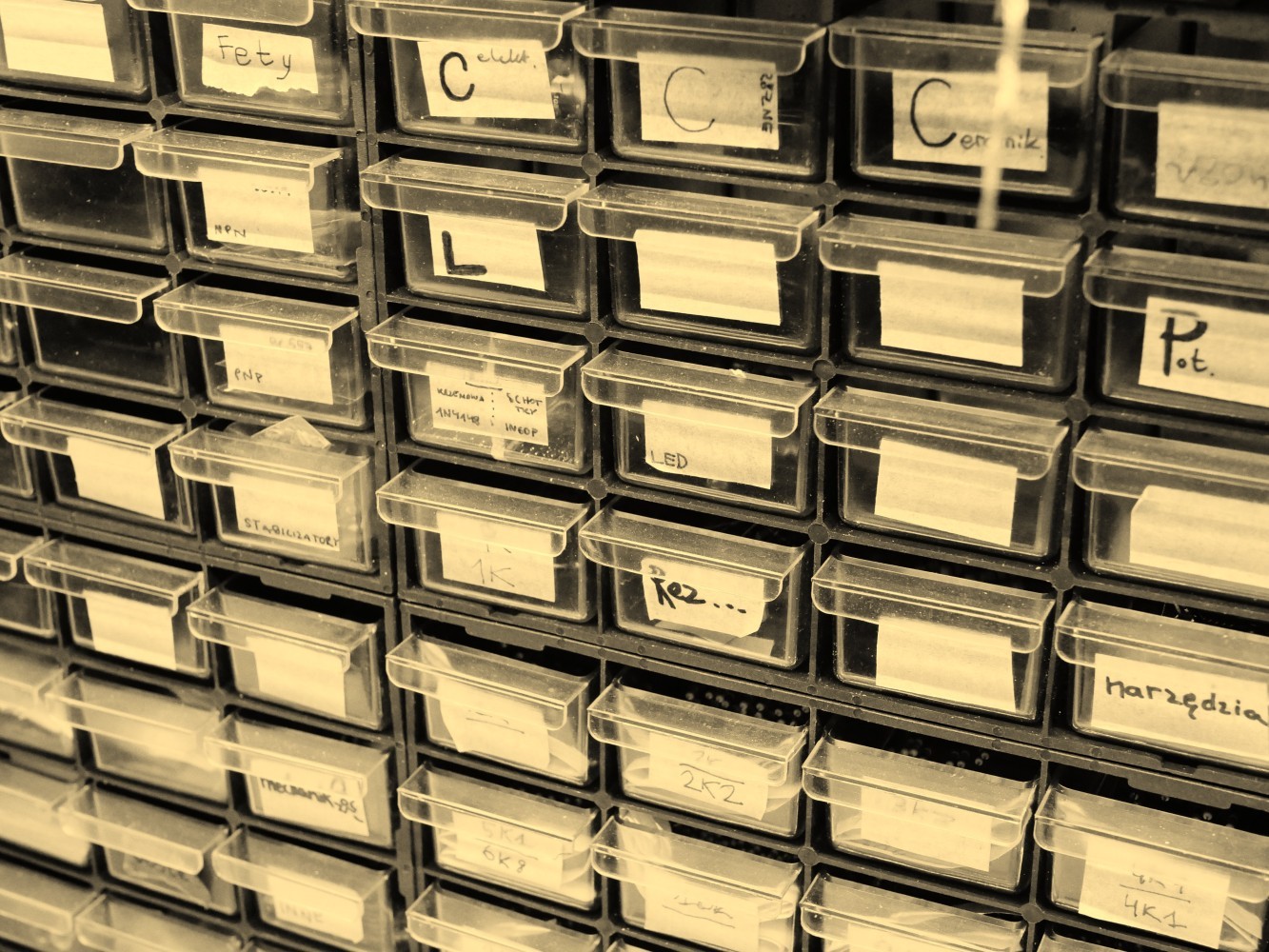
The integration solution between WM and the Service process comprises two key components:
1. Device Traceability: We have recorded the various locations in the workshop as ‘storage types’ in WM. Additionally, we created a generic location for technicians and used dynamic bins to create temporary locations. This enables us to generate reports showing how long a device has been at a particular spot.
2. Integration of Spare Parts: Technicians can indicate which parts they need for a repair. From there, a transfer order is created that specifies the correct batch. Using RFID scanners, the correct parts are selected.
Furthermore, we have utilized automation for administrative tasks and developed various extensions, such as scenario selection in Service Order for the creation of Transfer Orders and integration support with sales repair orders.
The result of this integration is a more efficient process with fewer errors and administrative burdens. It improves inventory counts, inventory management, and reduces the costs of spare parts. Moreover, it enhances the management of repairable devices, shortens repair times, and improves customer satisfaction through better communication.
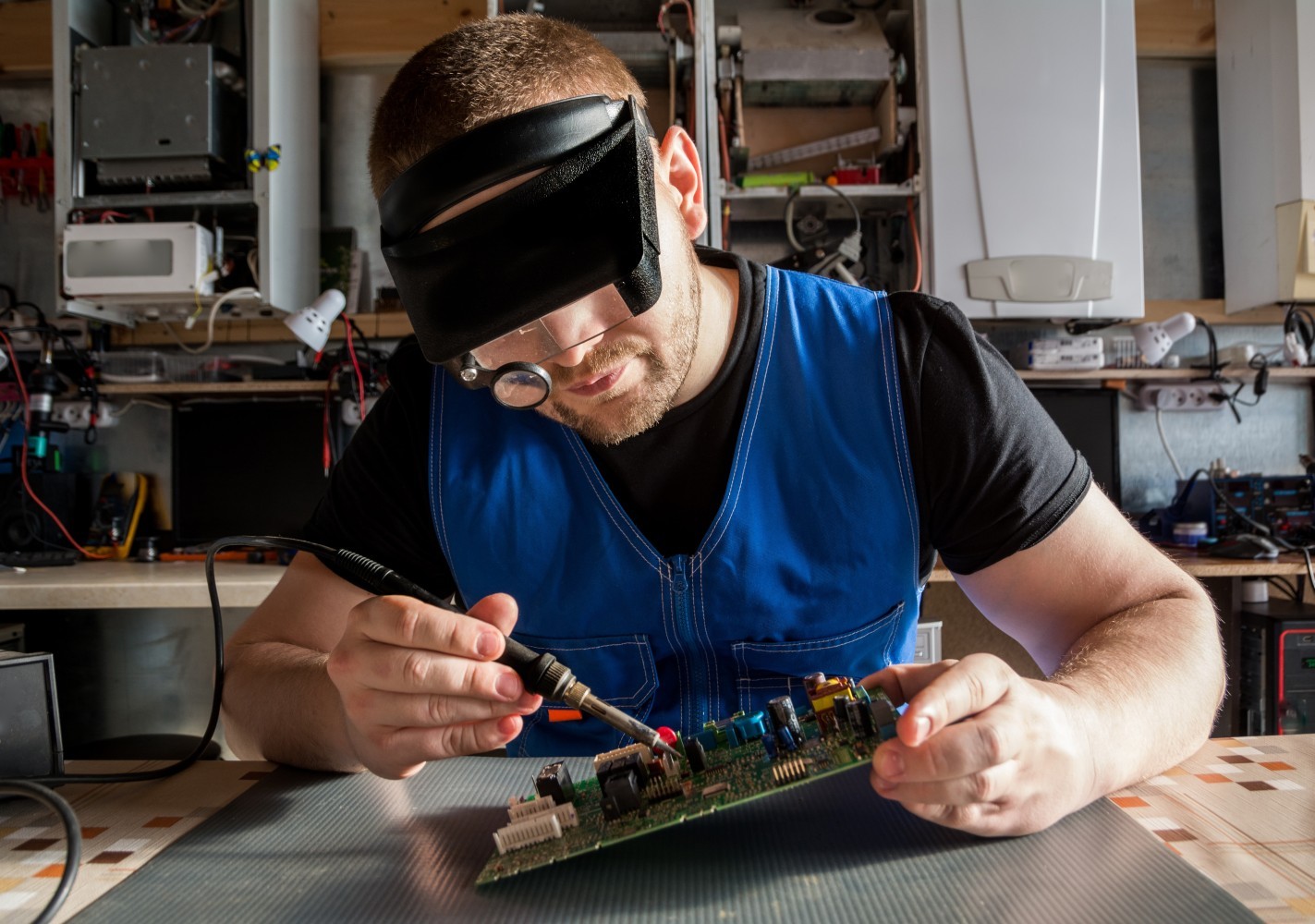
The integration of WM within the CS repair process illustrates the power of customization and integration. By thinking outside the box and creating bespoke solutions, we can make processes more efficient, effective, and customer-friendly.
Interested in delving deeper into the power of integration within the CS domain or do these challenges sound familiar? Please do not hesitate to contact Pascal Posthuma or Luuk te contacteren. We are eager to engage in a conversation.